ТЕХНОЛОГИЯ ПЕРЕРАБОТКИ КОММУНАЛЬНЫХ ОТХОДОВ
Краткое описание процесса беспламенной газификации образующихся коммунальных отходов на оборудовании комплексаСостав комплекса беспламенной газификации
В состав комплекса беспламенной газификации образующихся коммунальных отходов будут входить следующие основные блоки:-
Блок селекции загружаемого материала -
для сортировки поступающих отходов (отбора камней и песка, лома металлов, стекла и пищевых отходов с биомассой) -
Блок беспламенной газификации -
для выработки синтез-газа и кокса -
Блок биологического газа -
для переработки пищевых отходов и биомассы
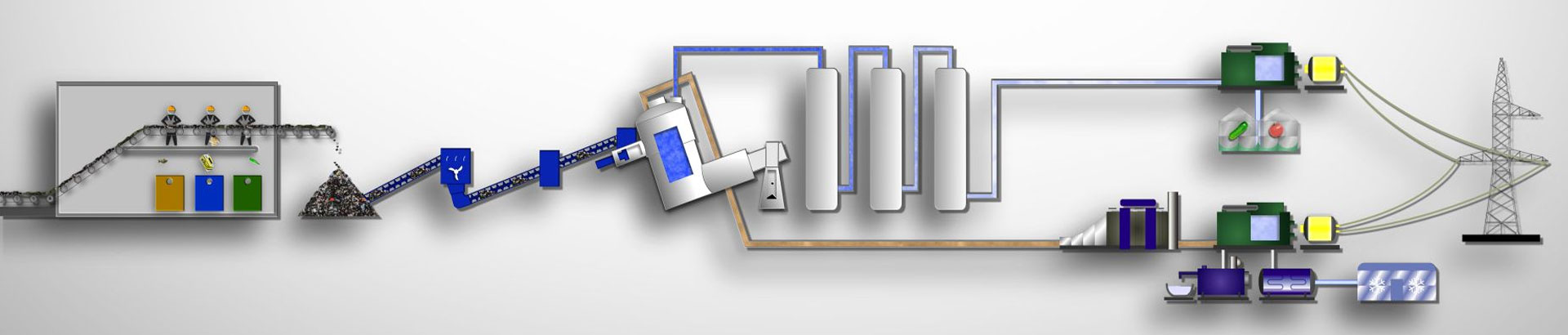
Блок селекции загружаемого материала (образующихся коммунальных отходов)
Блок селекции предназначен для сортирования и измельчения образующихся коммунальных отходов с целью их подготовки для модулей беспламенной газификации, выборки пищевых отходов и растительной массы для блока биологического газа с энергетическим оборудованием, а также отбора вторичного сырья в виде лома черных и цветных металлов, стекла для их последующей реализации на сторону. Параллельно будет производиться отсеивание инертных материалов в виде песка, камней и строительного мусора.Блок биологического газа с энергетическим оборудованием
Отсортированная часть сырья, в виде пищевых отходов и биомассы, имеет свои особенности, поэтому для их переработки требуется наличие дополнительного участка предварительной подготовки (измельчение, отделение неорганических включений и пастеризация).Накопление подобной части подготовленного сырья рассчитано на 1-2 дня и происходит в приемном резервуаре. После приемного резервуара пищевые отходы перекачиваются в реактор, в котором находятся от 8 до 10 суток. Там создаются специальные температурные условия от +25°С до + 28°С с соблюдением соответствующей по технологическому процессу влажности с контролем уровня рН.
Из реактора идет дозированная подача сырья в биологический блок для сохранения бактериального баланса в биологическом субстрате. Отработанный биологический субстрат загружается и разгружается автоматически.
После разгрузки биологический субстрат разделяют на твердые биологические удобрения и жидкие биологические удобрения.
Получаемый биологический газ собирается во внешних газгольдерах и используется для выработки требуемой для комплекса электрической и тепловой энергии.
Отведение биологического газа происходит по трубопроводу, который оснащен устройствами автоматического отвода конденсата и предохранительными устройствами, которые защищают газгольдер от превышения допустимого давления.
Из газгольдера биологический газ непрерывно подается на газовую поршневую установку для выработки электрической и тепловой энергии.
Управление работой всем блоком биологического газа с энергетическим оборудованием осуществляется по командам с центрального программного модуля.
Блок беспламенной газификации подготовленных отходов (термолиз)
Производственный процесс утилизации образующихся коммунальных отходов по технологии термолиза выглядит по схеме следующим образом.
Поступающие для переработки, подготовленные и отсортированные твердые бытовые отходы (без пищевых отходов и биомассы, а также без инертных материалов), складируются.
Со склада они формируются в загрузочные партии и подаются в установку газификации. Поступающие отходы (за счет прямого и косвенного их нагрева с помощью произведенного синтез-газа) повышаются в своей температуре, происходит испарение воды и отделяется кислород. Высушенные отходы через аппараты по шнекам поступают в многокаскадный реактор термолиза для беспламенной своей газификации при температуре от 400°С до 950°С.
Каждый реактор термолиза состоит из двух камер газификации. В ходе реакции беспламенной газификации образуется синтез-газ, который далее поступает в отделение обогащения газа и там же происходит его очистка от вредных примесей и побочных продуктов. Полукоксование и фумигация твердых бытовых отходов происходит в обеих камерах газификации при различных температурах. Нагрев, необходимый для процесса коксования, осуществляется с помощью грелок в камерах сгорания на внешнем кожухе реактора термолиза.
Контроль работы реакторов газификации и гарантия их безопасной эксплуатации реализованы с помощью ряда измерительных зондов и системы безопасности, сконцентрированной в единую диспетчерскую систему. Газопроводная система защищена от избыточного давления наличием надлежащего количества контрольно-измерительных мембран. В случае повышения внутреннего давления или в случае аварийной ситуации, образующийся газ отводится к факелу. Дополнительно имеется система обеспечения водой и водяным паром для моментальной остановки реакции газификации.
К реакторам газификации подсоединяется каскад из двух последовательных агрегатов коксования. В них происходит дальнейшее термическое разложение бытовых отходов вместе с первичным коксовым материалом для выделения синтез-газа. Как и реактор термолиза, агрегаты коксования снабжены обогревательным кожухом для прямого нагрева. Получаемый в итоге твердый остаток в виде кокса, который после соответствующего охлаждения с помощью пара и воды передаются в закрытые емкости.
В отделении обогащения синтез-газ проходит систему скрубберов, отделителей, емкостей и насосов. К каждому реактору подключен скруббер (установка абсорбционной очистки газа). После них газовые потоки обеих линий соединяются и направляются через каскады абсорбционной очистки, которые абсорбируют, при своей циркуляции, конденсат из коксующегося газа, одновременно охлаждая его. При технологии термолиза органические вещества распадаются на коротко цепные углеводороды, а окиси металлов, как и окиси других неорганических веществ (например, соединения окиси серы), редуцируются.
При очистке синтез-газа достигается полная конденсация алифатических и ароматических веществ. Содержание вредных примесей (к примеру, HCL) сокращается за счет нейтрализации известковой водой, с соблюдением предписанных требований.
Маслосодержащая рабочая среда и вода отделяются с помощью масляных сепараторов. Сточная вода дополнительно очищается активированным углем и биологической очисткой сточных вод установкой термолиза. После этого сточные воды могут выводиться в систему отвода сточных вод промышленных и производственных зон. Отходящий воздух процесса термолиза попадает в биологическую очистку отходящего воздуха. Для устранения эмиссии запахов отходящих газов, сопутствующих очистке сточных ввод и многоступенчатой сушке отходов, они отводятся из рабочих зон по системе трубопроводов с интегрированными биологическими прокладками.
Технологический газовый поток, после прохождения всех процессов очистки, попадает в хранилище газа. Хранилище газа служит для приема и буферизации синтез-газа, полученного в процессе термолиза, для обеспечения питания реакторов и агрегатов коксования, а также предназначается для отвода газа потребителю, с помощью компрессорной станции. Посредством обратного смешения выработанного газа, его качество из реакторных линий уравнивается. Получаемый синтез-газ идет по просьбе заказчика с применением дополнительного оборудования по опции либо на генерацию энергетических ресурсов, либо на производство разнообразной химической продукции.
Защитная система состоит из факела, который служит, в случае аварийной ситуации, надежным отводом синтез-газа из коксующей установки или из хранилища газа. Соединительные трубопроводы оснащены арматурой, которая при отключении энергообеспечения автономно открывается. Соединения реакторов газификации с факелом оснащены предохранительными мембранами для недопущения аварийного подъема давления.
Для питания установок используется сточная вода из систем водоподготовки, которая затем возвращается обратно. Органические остатки периодически изымаются и загружаются на установку термолиза. Система циркуляции воды для очистки технологического газа содержит охлаждающие установки, которые в контуре циркуляционного водоснабжения соединены с теплоносителем, работающим на воздухе окружающей среды.
СТАДИИ ПЕРЕРАБОТКИ ОТХОДОВ
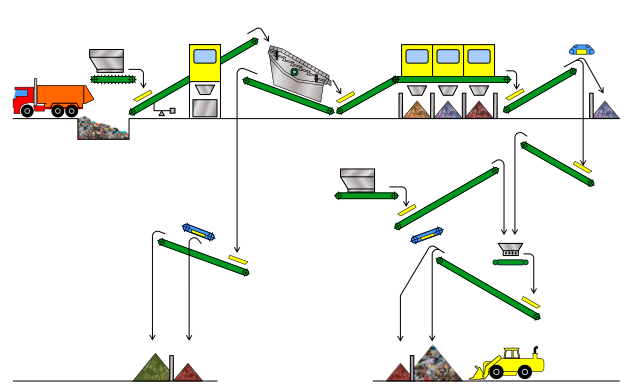
Стадия сортировки отходов
Сортирующая станция
предназначена для предварительной селекции образующихся коммунальных отходов с целью отбора пищевых отходов и биомассы, металла и стекла, камней, керамики, песка и бытового строительного мусора.
Поступающие отходы
Образующиеся коммунальные отходы временно складируется на площадке перед сортирующей станцией.
Загрузка
Одним погрузчиком отбираются отдельно крупногабаритные вещи (диваны, шкафы, телевизоры, мониторы компьютеров и т.д.). Другим погрузчиком осуществляется постоянная загрузка бытовых отходов в бункер накопитель для подачи на сортирующую станцию.
Вибрационное сито
Конвейер-подъемник транспортирует отходы из бункера накопителя на конвейер- распределитель, с которого эти подготовленные отходы попадают на шайбовое и вибрационное сито для просеивания мелкого материала (песок, камни, керамика и мелкий бытовой строительный мусор).
Станция ручной сортировки (1)
Материал с вибрационного сита попадается на сортировочный конвейер, расположенный в закрытой кабине сортировочной станции для селекции пищевых отходов и биомассы, стекла, остатка металлов после их улавливания до подачи на сортирующую станцию.
Станция ручной сортировки (2)
Отсортированное на конвейере вторичное сырье, в виде стекла и остатка металлов, а также пищевые отходы и биомасса, направляется на каждом рабочем месте в шахты для сброса материала.
Магниты
После проведения предварительного сортирования отходов в закрытой кабине ручным способом, входное сырье направляется через ряд магнитов для улавливания остающегося лома черных и цветных металлов. Обработка металлов Собранное вторичное сырье в виде лома черных и цветных металлов подлежит прессованию и упаковыванию.
Шредер
После проведения отбора лома черных металлов входное сырье по конвейеру подается на шредер, с целью измельчения прошедших стадию сортирования отходов до необходимых параметров, для дальнейшей поставки в реакторы беспламенной газификации.
Завершающий этап сортировки
Подготовленные и отсортированные бытовые отходы складируются на приспособленной для этих целей промышленной бетонированной площадке для последующей подачи его в блок беспламенной газификации.
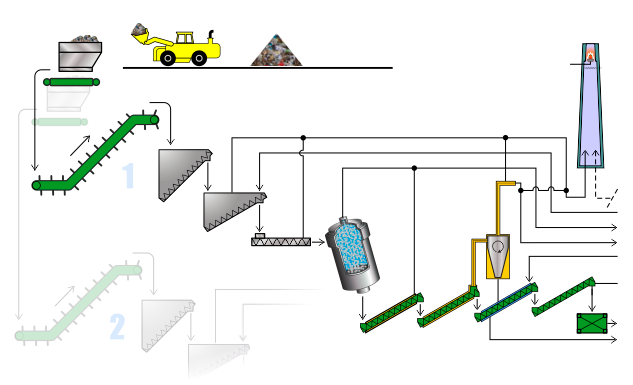
Стадия переработки сырья
Блок беспламенной газификации линия 1 и линия 2 Прошедшее стадию сортирования и измельчения до необходимых параметров сырье поступает с промышленной площадки на блок беспламенной газификации для выработки синтез-газа.
Подача подготовленного сырья в блок газификации Отсортированные и подготовленные отходы со склада на промышленной площадке формируются в загрузочные партии и подаются в блок беспламенной газификации.
Главный реактор и реактор второго уровня
Блок сепарации В присоединенном к реакторам беспламенной газификации блоке сепарации выработанный синтез-газ проходит очищение от мелких минеральных частиц и пыли
Блок безопасности Контроль работы реакторов термолиза и гарантия их безопасной эксплуатации реализованы с помощью ряда измерительных зондов и системы безопасности, сконцентрированной в единую диспетчерскую систему.
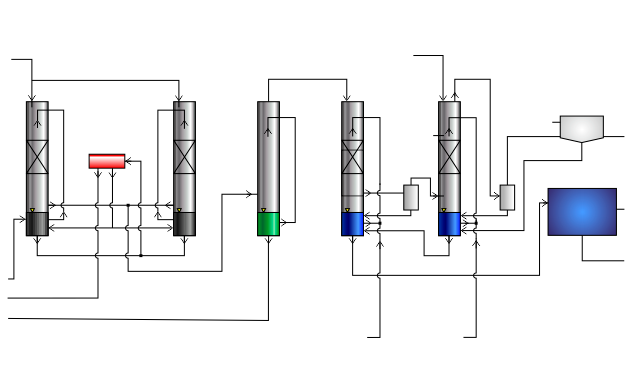
Стадия очистки синтез-газа
1 ступень очистки синтез-газа
В отделении обогащения выработанный синтез-газ проходит систему скрубберов, отделителей, емкостей и насосов. К каждому реактору подключен скруббер (установка абсорбционной очистки газа)..
2 ступень очистки синтез-газа
На второй ступени очистки синтез-газа происходит первичное уменьшение содержания в нем вредных примесей (к примеру, HCL) за счет нейтрализации известковой водой, с соблюдением предписанных требований.
3 ступень очистки синтез-газа
На третьей ступени происходит окончательная очистка синтез-газа от вредных примесей.
4 ступень очистки синтез-газа
На четвертой ступени очистки синтез-газа достигается полная конденсация алифатических и ароматических веществ. Во время последнего цикла вредные вещества и легкие частицы выводятся в связанном с рабочей средой состоянии.
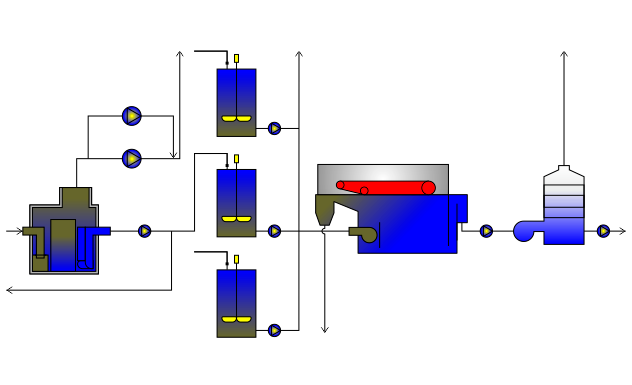
Очистка воды и отходящего воздуха
Сепаратор жидкой фракции, очистка воды
Маслосодержащая рабочая среда и вода после реакторов беспламенной газификации отделяются с помощью масляных сепараторов.
Очистка воды
В блоке водоочистки присутствующая в технологическом процессе сточная вода после реакторов термолиза дополнительно очищается активированным углем и биологической обработкой сточных вод. После этого сточные воды могут быть отведены в систему отвода сточных вод промышленных зон.
Очистка воды, воздушный стриппер
Блок воздушного стриппера используется для биологической очистки отходящего воздуха при проведении процесса термолиза, а также для устранения эмиссии запаха, сопутствующего очистке сточных вод.
Сравнительные показатели различных технологий утилизации и переработки образующихся коммунальных отходов
# | Показатели | Единицы измерения |
Технология | ||||
---|---|---|---|---|---|---|---|
Термическая переработка | Плазменная | Беспламенная газификация (термолиз) |
Компостирование (биологическая газификация) | ||||
* Сжигание |
** Пиролиз |
||||||
1 | Удельные эксплуата- ционные затраты |
евро/1т ТБО | 34-45 | 30-35 | 45-57 | 45-55 | 27-32 |
2 | Удельные экологические платежи | евро/1т ТБО | 2 | 2 | 1 | нет | 2 |
3 | Удельные доходы предприятия | евро/1т ТБО | 20 | 17 | 5 | 90-200 | 5 |
4 | Удельные энергетические затраты | КВт/1т ТБО | 50 - 70 | 50 - 70 | 500 | 65 | 90-120 |
5 | Удельная занимаемая площадь | м²/1т ТБО в год | 0,1-0,2 | 0,15-0,30 | 0,1-0,2 | 0,1 | 0,4-0,6 |
Экологические аспекты | |||||||
6 | Наличие отходов производства | % от массы ТБО | 23 - 28 (зола и шлак) | 25 -30 (коксовый остаток) | Мелко- дисперсная пыль, возгоны тяжелых металлов |
песок и камни от сортирования, золы и шлака нет | 20 - 25 (не компостируемые фракции) |
7 | Загрязнение почвы | только наличие отвала шлака | только коксовый остаток | практически нет | нет | практически нет | |
8 | Загрязнение грунтовых вод | нет | нет | нет | нет | нет | |
9 | Загрязнение атмосферы | в пределах норм | в пределах норм | тяжелые металлы | нет | в пределах норм | |
Получаемые продукты переработки ТБО | |||||||
10 | Энергия производимого пара *** | МВт/1 т ТБО | 160 | 120 | нет | нет | нет |
11 | Электроэнергия | МВт/1 т ТБО | 0,40 | 0,30 | 0,50 | 1,5-2,5 | нет |
12 | Компост | % от массы ТБО | нет | нет | нет | нет | 50 |
13 | Черный металл | -«- | 2 | 2 | 3 | 3 | 3 |
14 | Цветной металл | -«- | - | 0,3-0,4 | - | 0,3-0,4 | 0,3 -0,4 |
15 | Другое вторсырье | -«- | - | 5 -10 | 15 - 20 | Стеклобой 3-6 | 5- 10 |
* Технология сжигания рассмотрена на примере использования топочных устройств с колосниковыми решетками.
** В качестве технологии пиролиза рассмотрена система с пиролитическим реактором, работающим при средней температуре 850°С.
*** Производимый водяной пар используется для производства электроэнергии (собственное и внешнее потребление), технологических нужд и собственных нужд завода (отопление, вентиляция, ГВС)
Сравнение технологий: на примере действующего завода сжигания отходов в Баку (Азербайджан), проекта завода в Бурятии, и проекта завода по беспламенной газификации отходов
Таблица 2
Показатель | Единица измерения | * Мусоросжигательный завод IV поколения в Баку (Азербайджан). Построен французской компанией "CNIM S.A." | Проект внедрения комплекса беспламенной газификации THERMOTEC POWER | Проект завода Mitsubishi Heavy Industries Ltd в Бурятии |
---|---|---|---|---|
Мощность переработки отходов в год | Тонн | 500 000 | 240 000 | 240 000 |
Генерация электроэнергии | МВт/ч | 28 | 25 | 10,2 |
Использование природного газа в процессе производства | Да/Нет | Да | Нет | Да |
Остатки на захоронение | Да/Нет | Да | Нет | Да |
Количество создаваемых новых рабочих мест | Человек | 100 | 100 | 100 |
Приблизительная занимаемая площадь | Га | 20 | 4,5 | 7,0 |
* Ссылка на публикацию в сети Интернет (источник приведенных данных): http://vesti.az/news/119327
Сравнение технологии сжигания коммунальных и промышленных отходов с технологией беспламенной газификации указывает в пользу последней.