ТЕХНОЛОГИЯ БЕСПЛАМЕННОЙ ГАЗИФИКАЦИИ ДЛЯ ПЕРЕРАБОТКИ УГЛЯ (ТЕРМОЛИЗ)
Краткое введение в технологию Беспламенной газификации (метод термолиза)КОМПЛЕКС БЕСПЛАМЕННОЙ ГАЗИФИКАЦИИ
Основные блоки оборудования термолиза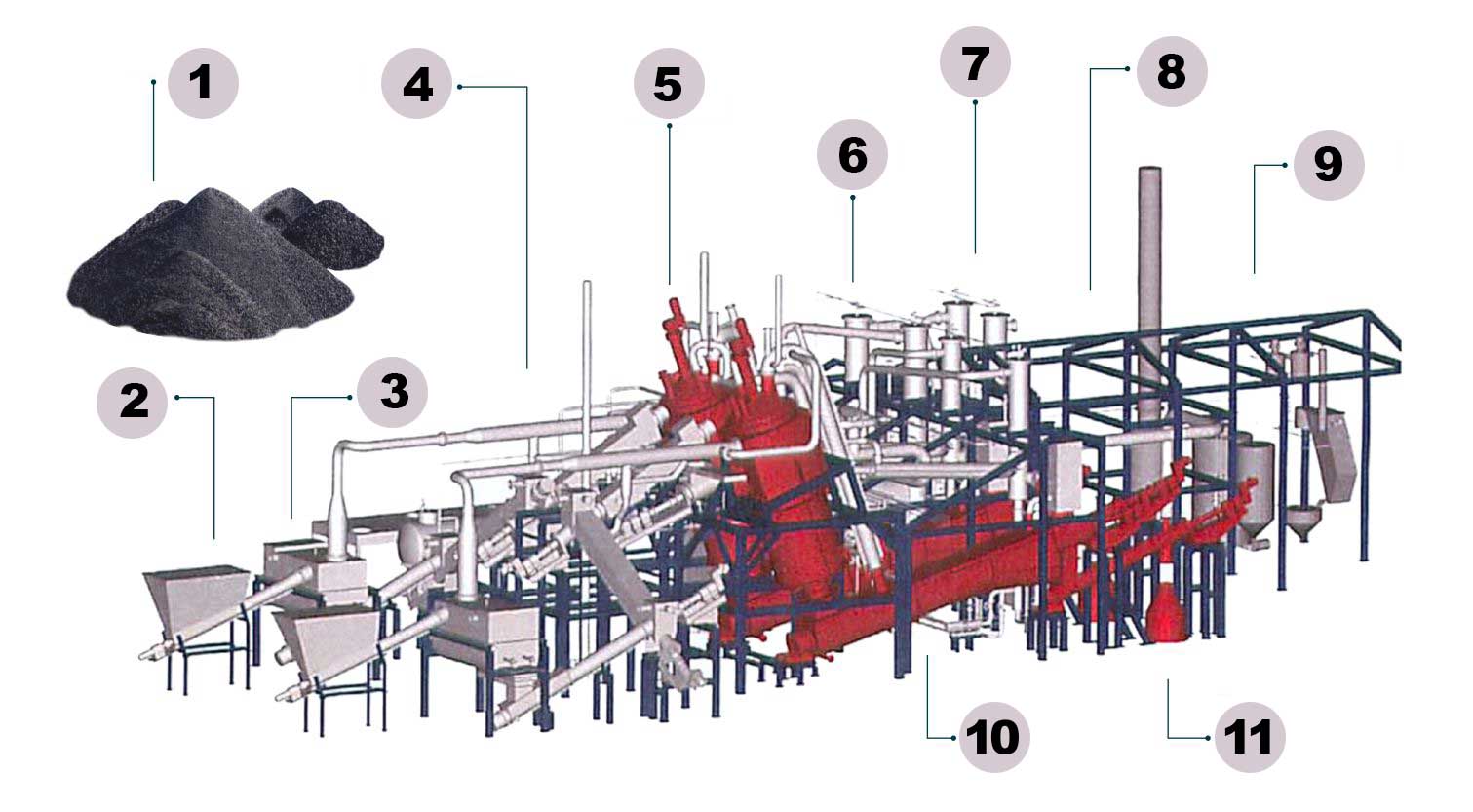
1 - сырье, 2 - подготовка и загрузка, 3 - первичная сушка, 4 - дополнительная сушка, 5 - реакторы термолиза (основные), 6 - полуяение и очистка газа, 7 - очищенный синтез-газ, 8 - очистка воды, 9 - хранилище газа, 10 - реакторы второго уровня, 11 - инертные материалы
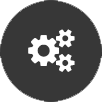
БЛОК ПОДГОТОВКИ СЫРЬЯ
для отбора минеральной составляющей и влаги из сырья, уменьшения содержания в сырье серы и измельчению сырья до требуемых по технологическому процессу размеров (не более 150 мм по наибольшей стороне)
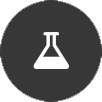
БЛОК ВЫПУСКА ХИМИЧЕСКОЙ ПРОДУКЦИИ ИЛИ ТОПЛИВА
для производства из синтез-газа целого ряда химической продукции или автомобильного топлива в соответствии с техническим заданием заказчика
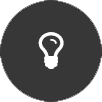
БЛОК ГЕНЕРАЦИИ ЭНЕРГЕТИЧЕСКИХ РЕСУРСОВ
для производства электрической и тепловой энергии из синтез-газа и кокса, вырабатываемых из сырья по технологии их беспламенной газификации в соответствии с техническим заданием заказчика
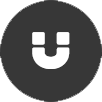
БЛОК ПО ОТБОРУ МЕТАЛЛОВ РАЗЛИЧНЫХ ГРУПП
для производства электрической и тепловой энергии из синтез-газа и кокса, вырабатываемых из сырья по технологии их беспламенной газификации в соответствии с техническим заданием заказчика
ОПИСАНИЕ ПРОЦЕССА (термолиз)
Производственный процесс переработки органического сырья в виде угля, торфа или горючих сланцев (далее сырье) по технологии термолиза выглядит по схеме следующим образом.Поступающее для переработки сырье (при необходимости проходит стадию обогащения и измельчения на блоке подготовки сырья), складируются. Со склада сырье формируется в загрузочные партии, а затем подаются по шнекам из загрузочного бункера в установку газификации. Поступающее сырье (за счет прямого и косвенного их нагрева с помощью произведенного синтез-газа) повышаются в своей температуре, происходит дополнительное испарение остатков воды и отделяется кислород.
Высушенное сырье через аппараты по шнекам поступают в многокаскадный реактор термолиза для беспламенной своей газификации при температуре от 400°С до 950°С. Каждый реактор термолиза состоит из двух камер газификации. В ходе реакции беспламенной газификации образуется синтез-газ, который далее поступает в отделение обогащения газа и там же происходит его очистка от вредных примесей и побочных продуктов. Полукоксование и фумигация сырья происходит в обеих камерах газификации при различных температурах. Нагрев, необходимый для процесса коксования, осуществляется с помощью грелок на внешнем кожухе реактора термолиза.
Контроль работы реакторов газификации и гарантия их безопасной эксплуатации реализованы с помощью ряда измерительных зондов и системы безопасности, сконцентрированной в единую диспетчерскую систему. Газопроводная система защищена от избыточного давления наличием надлежащего количества контрольно-измерительных мембран. В случае повышения внутреннего давления или в случае аварийной ситуации, образующийся газ отводится к факелу. Дополнительно имеется система обеспечения водой и водяным паром для моментальной остановки реакции газификации.
К реакторам газификации подсоединяется каскад из двух последовательных агрегатов коксования. В них происходит дальнейшее термическое разложение сырья вместе с первичным коксовым материалом для выделения синтез-газа. Как и реактор термолиза, агрегаты коксования снабжены обогревательным кожухом для прямого нагрева. Получаемый в итоге твердый остаток в виде кокса, который после соответствующего охлаждения с помощью пара и воды передаются в закрытые емкости. В отделении обогащения синтез-газ проходит систему скрубберов, отделителей, емкостей и насосов. К каждому реактору подключен скруббер (установка абсорбционной очистки газа). После них газовые потоки обеих линий соединяются и направляются через каскады абсорбционной очистки, которые абсорбируют, при своей циркуляции, конденсат из коксующегося газа, одновременно охлаждая его.
При технологии термолиза органические вещества распадаются на коротко цепные углеводороды, а окиси металлов, как и окиси других неорганических веществ (например, соединения окиси серы), редуцируются.
При очистке синтез-газа достигается полная конденсация алифатических и ароматических веществ. Содержание вредных примесей (к примеру, HCL) сокращается за счет нейтрализации известковой водой, с соблюдением предписанных требований.
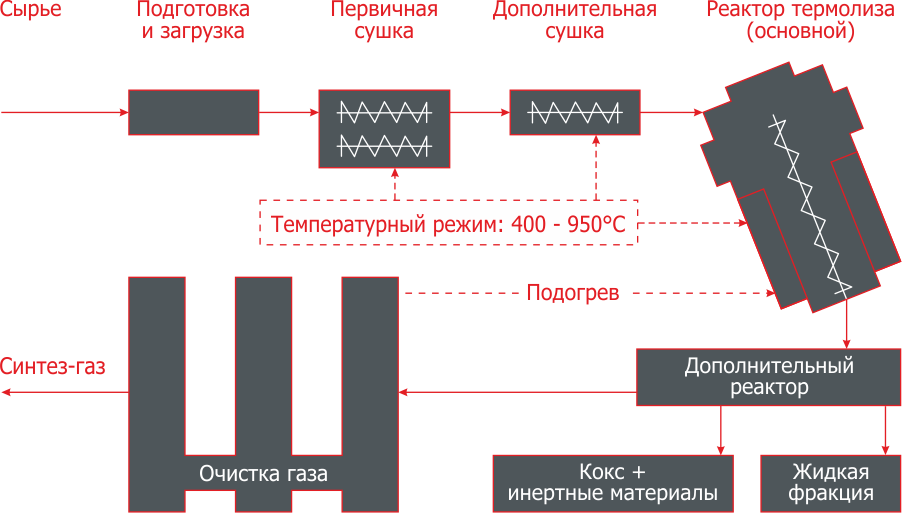
Отходящий воздух процесса термолиза попадает в биологическую очистку отходящего воздуха. Для устранения эмиссии запахов отходящих газов, сопутствующих очистке сточных вод и многоступенчатой сушке сырья, они отводятся из рабочих зон по системе трубопроводов с интегрированными биологическими прокладками.
Технологический газовый поток, после прохождения всех процессов очистки, попадает в хранилище газа. Хранилище газа служит для приема и буферизации синтез-газа, полученного в процессе термолиза, для обеспечения питания реакторов и агрегатов коксования, а также предназначается для отвода газа потребителю, с помощью компрессорной станции. Посредством обратного смешения выработанного газа, его качество из реакторных линий уравнивается.
Получаемый синтез-газ идет по просьбе заказчика с применением дополнительного оборудования по опции либо на генерацию энергетических ресурсов, либо на производство разнообразной химической продукции.
Защитная система состоит из факела, который служит, в случае аварийной ситуации, надежным отводом синтез-газа из коксующей установки или из хранилища газа. Соединительные трубопроводы оснащены арматурой, которая при отключении энергообеспечения автономно открывается. Соединения реакторов газификации с факелом оснащены предохранительными мембранами для недопущения аварийного подъема давления.
Для питания установок используется сточная вода из систем водоподготовки, которая затем возвращается обратно. Органические остатки периодически изымаются и загружаются на установку термолиза. Система циркуляции воды для очистки технологического газа содержит охлаждающие установки, которые в контуре циркуляционного водоснабжения соединены с теплоносителем, работающим на воздухе окружающей среды.
СТАДИИ ПЕРЕРАБОТКИ УГЛЕЙ И ГОРЮЧИХ СЛАНЦЕВ ПО ТЕХНОЛОГИИ БЕСПЛАМЕННОЙ ГАЗИФИКАЦИИ (ТЕРМОЛИЗА)
Стадия переработки сырья
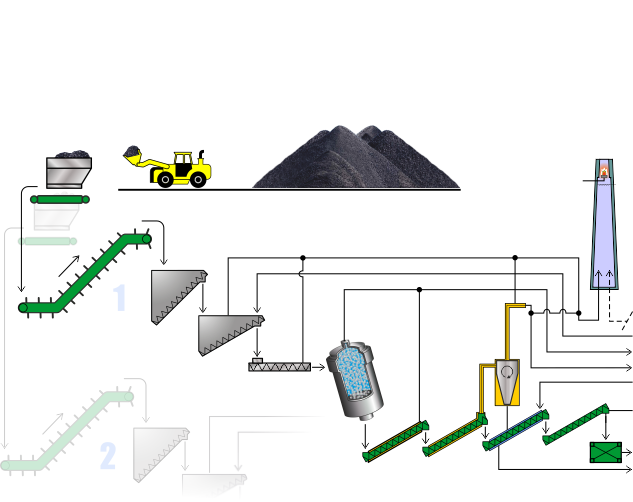
Блок беспламенной газификации линия 1 и линия 2
Прошедшее стадию сортирования и измельчения до необходимых параметров сырье поступает с промышленной площадки на блок беспламенной газификации для выработки синтез-газа.
Подача подготовленного сырья в блок газификации Отсортированные и подготовленные отходы со склада на промышленной площадке формируются в загрузочные партии и подаются в блок беспламенной газификации.
Главный реактор и реактор второго уровня
Блок сепарации
В присоединенном к реакторам беспламенной газификации блоке сепарации выработанный синтез-газ проходит очищение от мелких минеральных частиц и пыли
Блок безопасности
Контроль работы реакторов термолиза и гарантия их безопасной эксплуатации реализованы с помощью ряда измерительных зондов и системы безопасности, сконцентрированной в единую диспетчерскую систему.
Стадия очистки синтез-газа
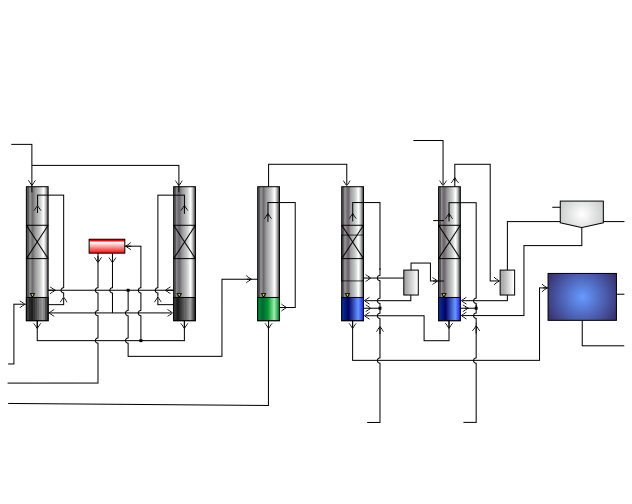
1 ступень очистки синтез-газа
В отделении обогащения выработанный синтез-газ проходит систему скрубберов, отделителей, емкостей и насосов. К каждому реактору подключен скруббер (установка абсорбционной очистки газа).
2 ступень очистки синтез-газа
На второй ступени очистки синтез-газа происходит первичное уменьшение содержания в нем вредных примесей (к примеру, HCL) за счет нейтрализации известковой водой, с соблюдением предписанных требований.
3 ступень очистки синтез-газа
На третьей ступени происходит окончательная очистка синтез-газа от вредных примесей.
4 ступень очистки синтез-газа
На четвертой ступени очистки синтез-газа достигается полная конденсация алифатических и ароматических веществ. Во время последнего цикла вредные вещества и легкие частицы выводятся в связанном с рабочей средой состоянии.
Стадия очистки воды и отходящего воздуха
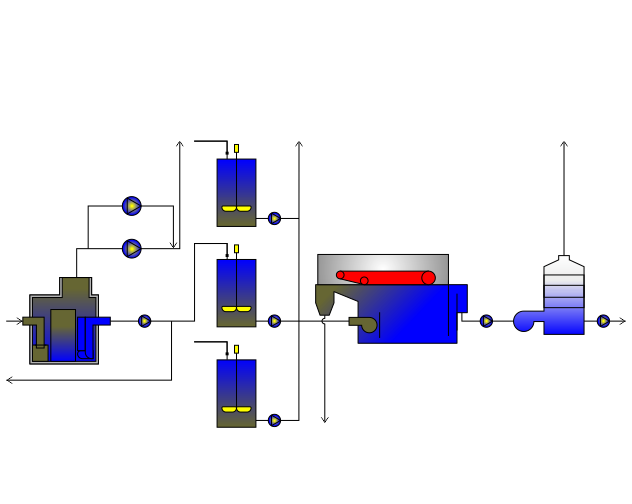
Сепаратор жидкой фракции, очистка воды
Маслосодержащая рабочая среда и вода после реакторов беспламенной газификации отделяются с помощью масляных сепараторов.
Очистка воды
В блоке водоочистки присутствующая в технологическом процессе сточная вода после реакторов термолиза дополнительно очищается активированным углем и биологической обработкой сточных вод. После этого сточные воды могут быть отведены в систему отвода сточных вод промышленных зон.
Очистка воды, воздушный стриппер
Блок воздушного стриппера используется для биологической очистки отходящего воздуха при проведении процесса термолиза, а также для устранения эмиссии запаха, сопутствующего очистке сточных вод.
Сравнение характеристик технологий переработки горючих сланцев
Таблица 1
Наименование технологии | |||||
---|---|---|---|---|---|
FUSHUN | Кивитер | Галотер (Enefit140, Petroter) |
PETROSIX | THERMOTEC | |
Страна | Китай | Эстония | Эстония | Бразилия | Германия |
Компания | разные | EESTI ENERGIA, VКG | EESTI ENERGIA, VКG | THERMOTEC POWER | |
Тип реторты | вертикальная | вертикальная | горизонтальная | вертикальная | наклонная |
Объем переработки сланца, тонн/день | 100 | 1 000 | 3 000 | 6200 и 1600 | блок один 520 |
Размер фракции, мм | 10 - 75 | 25 - 125 | 0 - 25 | 6 - 50 | 0 - 125 |
Выход смолы по Фишеру-Тропшу, % | 65 | 75 - 80 | 73 - 78 | 85 - 90 | -- |
Содержание углерода в золе, % | Н.Д. | 8,0 | 1,5 | Н.Д. | 0,01 |
Содержание влаги в золе, % | Н.Д. | 30,0 | 15,0 | Н.Д. | 1,0 - 3,0 |
Сравнение показателей по внедрению различных технологий переработки горючих сланцев
Таблица 2
FUSHUN | Галотер (Enefit140, Petroter) |
THERMOTEC | |
---|---|---|---|
Тип оборудования | FUSHUN | UТТ 3000 | THERMO 190 |
Компания | SINOPEC | EESTI ENERGIA, VКG | THERMOTEC POWER |
Объем переработки сланца, тонн/день | 3 000 * | 3 000 * | 3 000 * |
Размер фракции горючих сланцев на переработку, мм | 10 - 75 | 0 - 25 | 0 - 125 |
Производство товарной продукции: |
|
|
|
при ККД енергетичної установки 0,40 і переробці естонських сланців